Diesel engines are currently widely used in the automotive sector and in industry, due to their lower fuel consumption and their ability to exert high levels of torque compared to gasoline engines [1][2]. Despite the above, diesel engines expel pollutant emissions such as particulate matter, nitrogen oxides, and sulfur oxides through the exhaust gases, which cause serious environmental problems. Additionally, the presence of these pollutants causes negative effects on animal and human health [3][4]. In order to control the high levels of pollution, regulations have been established that force the reduction of emissions caused by fossil fuels. The problem of pollution by the exhaust gases of diesel engines is marked by the constant increase in their use due to the continuous industrialization and globalization of the world. Furthermore, as it comes from a non-renewable resource, there is an imminent risk of ending the oil reserves necessary for the production of fuels [5]. Due to the aforementioned problems (pollution and scarcity), efforts have been devoted to researching new alternative fuel sources.
Among the options investigated, biodiesel seems to be the most promising alternative to replace part of the diesel content [6]. Biodiesel is derived from animal fats and vegetable oils. Biodiesel fuel produced from vegetable oils has different positive characteristics such as its biodegradability, zero toxic, renewable, free of aromatics, and without sulfur content [7][8]. There are various investigations focused on the study of blends of commercial diesel with pure biodiesel. Among these studies, biodiesel obtained from soybean oil (SB) has been considered an attractive material since it is readily available in several countries and has a high percentage of oil derivation. Furthermore, its economic cost is low compared to other types of biodiesel from vegetable oils [9][10]. Canakci [11] concluded that the replacement of 20% of commercial diesel with biodiesel from soybean oil produces a reduction in emissions of CO, HC, and particulate matter, due to the high percentage of oxygen in biodiesel that improves the air-fuel ratio. Despite these advantages, research reports that the use of soybean oil biodiesel produces an increase in NOx and brake specific fuel consumption (BSFC) emissions by 11.2% and 13.8%, respectively. These negative results are consequences of the increased presence of oxygen, which favors the formation of NOx [12][13]. Additionally, the lower calorific value in the mixture with biodiesel causes a reduction in the maximum values of pressure in the chamber and in the net rate of heat release compared to commercial diesel. In general, these negative effects on combustion characteristics and NOx emissions are reported in the investigations by Randazzo and Sodre [14], Lin et al. [15], and Vellaiyan et al. [16].
Investigations of fuel blends with other types of biodiesel, such as palm-olein oil [17], mustard oil [18], jatropha oil [10], and castor oil [19], maintain the negative effect of causing an increase in fuel consumption and NOx emissions. To reduce these effects, researchers have studied emission control techniques using preprocessing and postprocessing. Among these techniques, it has been observed that the inclusion of water in fuel blends can lead to a reduction in fuel consumption and an increase in engine performance [20][21]. This is due to the fact that the water particles favor the blend between the fuel and the air, which allows a more complete combustion [22]–[24]. The improvement in the combustion process due to the presence of water particles allows to reduce the BSFC, thus increasing the thermal efficiency of the engine [25]. Additionally, the high latent heat of the water particles could cause a reduction in the temperature of the combustion flame. This could mitigate the formation of polluting emissions such as NOx, soot and particulate matter [26]–[28].
Research by Vellaiyan et al. [29] and Ithinin et al. [26] show that water emulsions in diesel cause a reduction in peak flame temperature. Additionally, it is reported that the addition of 10% water in the fuel allows the BSFC to be reduced by 11% compared to conventional diesel. Fahd et al. [30] carried out a series of experimental tests in which the emissions of an engine fed with 10% water were studied. The results report a reduction of 29-37% in NO emissions. This was attributed to the reduction of the adiabatic temperature due to the absorption of heat from the water particles. The reduction of NO contributes directly to the reduction of NOx formations. Similar results were reported by Alahmer et al. [31], which indicate a greater reduction in NOx emissions with the increase in the percentage of water in the fuel. Park et al. [32] obtained a 90% reduction in NOx as a result when using water emulsions with a percentage of 40%. Ghojel et al. [33] managed to achieve a 30% reduction in NOx when using emulsified fuels. Kaliaperumal and Udayakumar [34] reported a reduction between 10-25% of NOx emissions with water concentrations of 10-20%. Matheaus et al. [35] added 20% of water to conventional diesel, achieving a 19% decrease in NOx. Most research indicates that adding water to commercial diesel reduces NOx formation. Due to these results, researchers have studied the influence of the addition of water in biodiesel blends. Among the types of biodiesel investigated are Jatropha oil [36], Thevetia peruviana [37] and residual cooking palm oil [38]. In each of the above cases, a decrease in NOx emissions has been reported. Perumal and Ilangkumaran [39] analyzed blends of biodiesel from Pongamia with water emulsions in 5% and 10%. The results obtained indicate a reduction of 20% and 30% in NOx emissions.
Previous research shows that the addition of water has the potential to reduce NOx emissions, thus solving one of the main problems associated with the use of biodiesel. In the present study, the effect of water emulsions in soybean oil biodiesel is investigated. Because this oil has a high potential as a raw material for the production of biodiesel and the influence of water on this type of biodiesel has been little investigated in the literature. To analyze the potential of water emulsions in soybean oil biodiesel blends, combustion characteristics such as combustion chamber pressure, heat release rate, and BSFC are analyzed. Additionally, an evaluation is carried out on the emissions of CO, HC, NOx and smoke opacity. The development of the experimental tests is carried out in a single cylinder stationary diesel engine, to which blends of soybean oil biodiesel with 4% and 8% water emulsions were added. Each of these blends is compared to commercial diesel.
II. THEORETICAL FRAMEWORK
Water emulsions produce two main effects in the combustion chamber, which correspond to the phenomenon of reducing the temperature in the combustion chamber and the phenomenon of micro-explosions. These effects influence the characteristics and the combustion process [40]. Each of the phenomena are detailed below.
The phenomenon of temperature reduction in the combustion chamber is produced by the absorption of heat from the water particles. This is due to the fact that water has a lower boiling point compared to diesel, which causes that in fuels with water emulsions there is an additional absorption of heat, and therefore a decrease in temperature [41][42]. NOx emissions are directly related to the high temperatures in the chamber. Due to the above, the temperature reduction caused by the water emulsions could reduce the formation of NOx.
The phenomenon of micro-explosions is a consequence of small water droplets dispersed in the fuel. During the combustion process the water droplets produce micro-explosions, which favor the mixing process between the fuel and the air. This can lead to greater efficiency in the combustion process, reducing polluting emissions such as HC and particulate matter [43]–[45].
III. METHODOLOGY OR PROCEDURES
A two-stage transesterification process was used to prepare biodiesel from soybean oil, following the steps recommended in the research by Vellaiyan [6]. Figure 1 describes the steps to take soybean oil to biodiesel.

Figure 1: Schematic diagram of biodiesel preparation.
Source: Own creation based on contributions from [6].
The process begins with a reduction in the acid number of crude soybean oil through an esterification process. Subsequently, the crude soybean oil was mixed with 1% sulfuric acid and ethanol. The resulting mixture was stirred for 60 minutes at a temperature of 60 °C. Through a sedimentation process, the amount of unwanted methanol and water is removed. The resulting solution was applied to the transesterification process. For this, it was heated to a constant temperature of 60 °C and mixed with methanol and a solution of potassium hydroxide. Finally, a sedimentation process is carried out to separate the biodiesel from soybean oil.
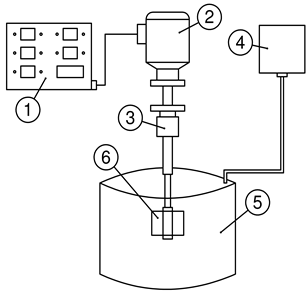
Figure 2: Schematic diagram of biodiesel preparation.
Source: Own elaboration.
1. Auto-Transformer, 2. Electric motor, 3. Gear box, 4. Water tank, 5. Mixing chamber, 6. Agitator.
To prepare biodiesel from soybean oil emulsified in water, the sorbitan monolaurate surfactant technique and a mechanical agitation process were used. Figure 2 shows the equipment used for this preparation.
To carry out the emulsification process, water is added slowly in drop forms to the biodiesel, with a mechanical stirring speed of 5000 rpm. The mixture was stirred for 45 minutes, and subsequently, a purification process was carried out using a filter. Because excess water causes engine failure, its concentration remained below 10%. Table 1 shows the composition and nomenclature of the fuels to be analyzed.
For the development of the experimental tests, a single-cylinder, 4-stroke stationary diesel engine was used. The technical characteristics of the engine are shown in Table 2.
Table 1: Test fuels.
Nomenclature |
Composition |
D |
100% Diesel |
SB |
95% Diesel + 5% Soybean oil biodiesel |
SB4W |
91% Diesel + 5% Soybean oil biodiesel + 4% water |
SB8W |
87% Diesel + 5% Soybean oil biodiesel + 8% water |
Source: Own elaboration.
Table 2: Specifications of the diesel engine.
Model |
SK-MDF300 |
Manufacturer |
SOKAN |
Bore x stroke |
78 mm |
Cycle |
4 Strokes |
Stroke |
62.57 mm |
Intake system |
Naturally Aspirated |
Injection Angle |
20° BTDC |
Injection system |
Direct injection |
Compression |
20:1 |
Displaced volume |
299 CC |
Source: Own elaboration.
Figure 3 shows the schematic diagram of the engine test bench. A dynamometer was used to check the engine operating conditions.
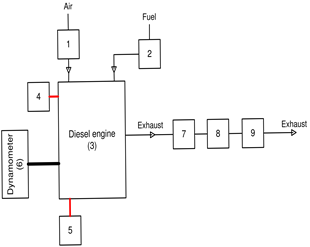
Figure 3: Engine test bench.
Source: Own elaboration.
1. Air flow meter, 2. Gravimetric fuel meter, 3. Diesel engine, 4. Piezoelectric sensor, 5. Encoder, 6. Dynamometer, 7. BrainBee AGS-688, 8. Bacharach PCA 400, 9. BrainBee OPA-100.
The intake flow and fuel flow measurements were made using a hot wire meter (BOSCH 22680 7J600) and a gravimetric flow meter. A piezoelectric sensor (KISTLER type 7063-A) was used to measure the combustion pressures. Exhaust gas emission levels were measured using the Bacharach PCA® 400 and BrainBee AGS-688 gas analyzers. Additionally, an opacimeter (BrainBee OPA-100) was used. A computer was used to record the measured parameters. Table 3 shows the specifications of the emission measurement instruments.
Four different operating conditions were selected for the experimental tests, in which the engine torque took values of 2 Nm, 4 Nm, 6 Nm, and 8 Nm at a constant rotation engine speed of 3400 rpm. In each of these conditions, the engine operated for 15 minutes to guarantee a stable condition in the measured parameters. Furthermore, in order to avoid experimental errors, each operating condition was repeated nine times.
Table 3: Gas analyzer specifications.
Instrument |
Measured quality |
Measuring range |
Resolution |
BrainBee AGS-688 |
CO |
0÷9.99 vol% |
0.01% vol |
CO2 |
0÷19.99 vol% |
0.1% vol |
HC |
0÷19.999 [ppm] |
1% vol |
Bacharach PCA 400 |
NOx |
0÷3000 [ppm] |
1 ppm |
Source: Own elaboration.
To analyze the characteristics of combustion when using water emulsions in soybean oil biodiesel, the calculation of the heat release rate (HRR) is performed. For this calculation, the differential model is used as a function of the crankshaft angle developed by Ferguson and Kirkpatrick [46]. The model used is described by means of Eq. (1).

where
is the heat release rate, P the combustion chamber pressure,
the crankshaft angle and V the cylinder volume. represents the specific heat ratio, which is defined by the Zucrow and Hoffman equation [47]. Due to the above, Eq. (2) is used.

Table 4 shows the uncertainties of the main measurement parameters.
Table 4: Uncertainty list of main measures.
Measure instrument |
Uncertainty (%) |
Dynamometer load |
±0.25 |
Pressure |
±0.05 |
Crank angle encoder |
±0.05 |
Brake specific fuel consumption |
±1 |
CO |
±0.1 |
HC |
±0.25 |
NOx |
±0.2 |
Source: Own elaboration.
IV. RESULTS, ANALYSIS AND INTERPRETATION
a. Properties of test fuels
The EN590 and EN4214 measurement standards were used to measure the physicochemical properties of palm oil biodiesel and water emulsions. The properties obtained are shown in Table 5.
Table 5: Test fuel properties.
Fuel |
Calorific value [MJ/kg] |
Viscosity [mm2/s] |
Density [kg/m3] |
D |
43 |
2.4 |
831 |
SB |
38 |
3.9 |
870 |
SB4W |
36.5 |
4.3 |
876 |
SB8W |
35 |
4.92 |
883 |
Source: Own elaboration.
The results shown in Table 5 indicate that the calorific value of SB is 11.62% lower compared to commercial diesel. The presence of water in SB4W and SB8W fuels causes the calorific value of the fuel to be further reduced. The fuels SB4W and SB8W presented a calorific value of 3.94% and 7.89% lower compared to the SB. Additionally, it was observed that SB4W and SB8W fuels show higher levels of density and viscosity. SB4W and SB8W water emulsion fuels produce a 10.25% and 26.15% increase in viscosity when compared to SB. This increase is associated with the high interaction that occurs in the water particles. On average, water emulsions show a density of 5.83% higher compared to diesel.
b. Combustion characteristics
Figure 4 shows the influence of test fuels on the pressures of the combustion process. The results indicate that the fuels with the water content (SB4W and SB8W) reach higher pressure levels during combustion, compared to SB. The SB4W fuel reached pressure conditions very close to commercial diesel.
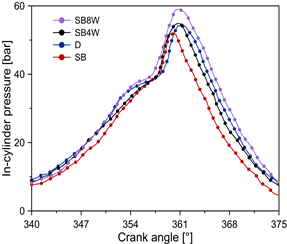
Figure 4: Pressure in the combustion chamber with 4 Nm and 3400 rpm.
Source: Own elaboration.
The maximum pressure values were 54, 51, 54.5, and 58 bar for fuels D, SB, SB4W, and SB8W, respectively. This increase in SB4W and SB8W fuels is attributed to the fact that the presence of water leads to a longer duration in micro explosions. The described behavior is in agreement with other types of biodiesel mixed with water [17][19].
The influence of fuels on the heat release rate (HRR) is shown in Figure 5. The results obtained indicate that the SB presents a reduction in the maximum value of HRR compared to diesel, which is mainly a consequence of its lower calorific value.

Figure 5: Heat release rate with 4 Nm and 3400 rpm.
Source: Own elaboration.
However, the addition of water in soybean oil biodiesel increases the maximum HRR value. In the case of the SB4W and SB8W blends, the maximum HRR value was found to be 5% and 20% higher compared to diesel. This is attributed to the heat absorption capacity of the water particles, which is subsequently released [30].
c. Fuel consumption
Changes in the Brake Specific Fuel Consumption for diesel and biodiesel blends are shown in Figure 6. As expected, soybean oil biodiesel causes an average increase in BSFC of 27% compared to diesel. This can be attributed to the viscosity and density properties of the SB since, as they are higher, they affect the spraying process by injecting a greater amount of fuel.
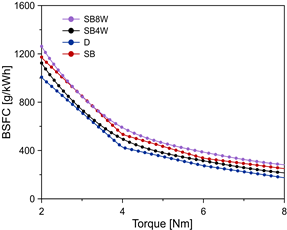
Figure 6: Brake Specific Fuel Consumption.
Source: Own elaboration.
In the case of emulsions in water, SB4W, and SB8W, two behaviors are shown. For SB4W fuel, the BSFC was reduced by 8.15% compared to the SB. However, SB8W fuel causes an increase in BSFC by 11% compared to SB. This reduction in the BSFC when adding a percentage of water is in agreement with the results present in other investigations [27]. However, a high percentage of water in the fuel causes a higher BSFC because the water particles cause longer combustion and a longer delay in ignition.
d. Emission characteristics
The smoke opacity of each fuel is shown in Figure 7. The results obtained show that soybean oil biodiesel causes a 16.44% reduction in smoke opacity when compared to commercial diesel. This result is contributed to the lower percentage of oxygen and carbon in the SB. Additionally, it was observed that the addition of a percentage of 4% and 8% of the water in biodiesel causes a greater reduction in smoke opacity. On average, the SB4W and SB8W have 13% less smoke opacity than the SB. This can be attributed to the better air-fuel ratio caused by the presence of water particles.
Nitrogen oxide (NOx) emissions are shown in Figure 8. It is observed that the SB causes a 15% increase in NOx emissions. This is a common behavior that has been reported in different types of biodiesel [48]. However, the presence of water allowed the reduction of NOx emissions. The results indicate that the SB4W and SB8W blends achieve a 14% and 33% decrease in NOx levels compared to commercial diesel. This behavior is mainly attributed to the reduction of the temperature in the combustion chamber caused by the heat absorption of the water particles.
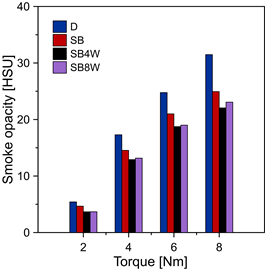
Figure 7: Smoke emissions for fuels tested.
Source: Own elaboration.

Figure 8: NOx emissions for fuels tested.
Source: Own elaboration.
Carbon monoxide (CO) and hydrocarbon (HC) emissions are shown in Figure 9 and Figure 10. The results shown in Figure 9 indicate that soybean oil biodiesel reduces CO emissions by 36% compared to diesel. For low levels of torque, it was observed that the water emulsions present higher emission levels than the SB. This may be due to a reduction in temperature during the combustion process, which leads to incomplete combustion at low load levels. However, for torque greater than 2 Nm, it was observed that the SB4W fuel achieves a 15% greater reduction compared to the SB. Although the SB8W fuel has lower CO emissions compared to diesel, it is not possible to obtain a greater reduction than the SB.
Similar behavior was observed when analyzing HC emissions (Figure 10). In general, soybean oil biodiesel shows an improvement in HC emissions under all operating conditions. Water emulsions show less reduction capacity for low torque levels. However, for higher load levels, the SB4W fuel allows a 40% greater reduction than the SB. Again, this behavior is not reflected in SB8W fuel.
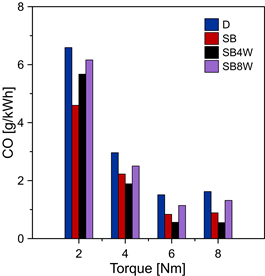
Figure 9: CO emissions for fuels tested.
Source: Own elaboration.
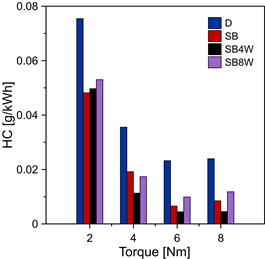
Figure 10: HC emissions for fuels tested.
Source: Own elaboration.
V. PROPOSAL FOR IMPROVEMENT
Although the 4% and 8% water emulsions in the soybean oil biodiesel made it possible to reduce the emissions of smoke opacity, NOx, CO and HC, it was observed that the addition of water causes an increase in the consumption of fuel compared to conventional diesel. To minimize this effect, several methods can be implemented such as adjusting the injection time, oxygen enrichment and the addition of nanoadditives (ferric chloride and aluminum oxide). This last alternative is frequently investigated today.
The research carried out has focused mainly on the study of emissions and combustion characteristics. However, the study can be completed by considering the economic analyzes for water emulsions applied to soybean oil biodiesel, the development of more efficient blending processes, and the long-term effects of water emulsions on engine components.
VI. CONCLUSIONS
This study analyzes the influence of biodiesel from soybean oil and water emulsions (4% and 8%) on the performance conditions, combustion characteristics, and polluting emissions of a diesel engine. The experimental results obtained show that the presence of water particles in soybean oil biodiesel causes a reduction in calorific value and an increase in density and viscosity. On average, SB4W and SB8W water emulsions produce a 6% reduction in calorific value, and an 18% and 1% increase in viscosity and density, compared to SB.
The addition of water in soybean oil biodiesel allows maximum values to be produced in the pressure and release rate curves that are closer to those obtained with commercial diesel, which is a consequence of the ability of water particles to produce micro explosions and absorb heat. The inclusion of an adequate percentage of water in soybean oil biodiesel allows improving fuel consumption. In the case of the SB4W fuel, a reduction in the BSFC of 8.15% compared to the SB was observed. However, a percentage of water greater than 4% can cause an inverse behavior. This effect can be reduced by applying techniques such as adjusting the injection time, oxygen enrichment and the addition of nanoadditives.
The study of emissions showed that fuels with water content reduce NOx levels. On average, the SB4W and SB8W allow this type of emissions to be reduced by 23%. Despite the fact that both water emulsions reduce the emissions of the opacity of smoke, CO and HC compared to diesel. The SB4W fuel had a greater capacity to reduce these emissions compared to the SB8W. This is due to the fact that a high concentration of water particles can cause an excessive reduction in temperature, which can lead to incomplete combustion.
In the specific case of SB4W fuel, it is possible to achieve a reduction of 16%, 29%, and 14% in emissions of CO, HC, and smoke opacity compared to biodiesel from soybean oil. Due to the previous results, the inclusion of 4% of the water in soybean oil biodiesel is recommended to improve emissions of NOX, the opacity of smoke, HC, and CO.
VII. RECOMMENDATIONS
Since the condition of the engine components has a direct impact on performance, it is necessary to verify that the presence of water does not cause damage by corrosion processes. Therefore, it is advisable to analyze which components are exposed to this risk and determine the exposure time.
One of the main limitations for the application of fuels with water emulsions is the little support from governments for this type of alternative fuels. Therefore, future research should focus on engines used in the transport sector and in the industrial sector. This in order to demonstrate the advantages of water emulsions in biodiesel blends in different types of applications.
VII. REFERENCIAS
[1] G. Valencia-Ochoa, J. Duarte-Forero, and C. Acevedo-Peñaloza, “Caracterización de la tasa de liberación de calor en los cilindros de un motor de generación a gas natural de 2 MW,” Aibi Rev. investig. adm. ing, vol. 8, no. 1, pp. 5–11, Jan. 2020.
[2] J. C. Acevedo-Páez, N. A. Urbina-Suárez, A. Z. Acevedo-Rodríguez, and L. C. Becerra-Orozco, “Study of the production of biodiesel by enzymatic and chemical processes from used cooking oil,” Aibi Rev. investig. adm. ing, vol. 7, no. 2, pp. 20–25, Jun. 2019.
[3] F. Posso, J. C. Acevedo Paez, and J. Hernández, “El impacto económico de las energías renovables,” Aibi Rev. investig. adm. ing, vol. 2, no. 2, pp. 22–26, Jul. 2014.
[4] W. Pardavé Livia and J. Jerez Pérez, “Valoración económica de la calidad de aire y su impacto en registros epoc de Bucaramanga,” Aibi Rev. investig. adm. ing, vol. 2, no. 2, pp. 13–18, Jul. 2014.
[5] Y. Devarajan, D. B. Munuswamy, and A. Mahalingam, “Influence of nano-additive on performance and emission characteristics of a diesel engine running on neat neem oil biodiesel,” Environ. Sci. Pollut. Res., vol. 25, no. 26, pp. 26167–26172, Sep. 2018.
[6] S. Vellaiyan, “Enhancement in combustion, performance, and emission characteristics of a biodiesel-fueled diesel engine by using water emulsion and nanoadditive,” Renew. Energy, vol. 145, pp. 2108–2120, Jan. 2020.
[7] A. S. Silitonga et al., “Evaluation of the engine performance and exhaust emissions of biodiesel-bioethanol-diesel blends using kernel-based extreme learning machine,” Energy, vol. 159, pp. 1075–1087, Sep. 2018.
[8] X. Yuan et al., “Applications of bio-oil-based emulsions in a DI diesel engine: The effects of bio-oil compositions on engine performance and emissions,” Energy, vol. 154, pp. 110–118, Jul. 2018.
[9] O. Özener, L. Yüksek, A. T. Ergenç, and M. Özkan, “Effects of soybean biodiesel on a DI diesel engine performance, emission and combustion characteristics,” Fuel, vol. 115, pp. 875–883, Jan. 2014.
[10] A. S. Silitonga, M. H. Hassan, H. C. Ong, and F. Kusumo, “Analysis of the performance, emission and combustion characteristics of a turbocharged diesel engine fuelled with Jatropha curcas biodiesel-diesel blends using kernel-based extreme learning machine,” Environ. Sci. Pollut. Res., vol. 24, no. 32, pp. 25383–25405, Nov. 2017.
[11] M. Canakci, “Combustion characteristics of a turbocharged DI compression ignition engine fueled with petroleum diesel fuels and biodiesel,” Bioresour. Technol., vol. 98, no. 6, pp. 1167–1175, Apr. 2007.
[12] S. S. Reham, H. H. Masjuki, M. A. Kalam, I. Shancita, I. M. Rizwanul Fattah, and A. M. Ruhul, “Study on stability, fuel properties, engine combustion, performance and emission characteristics of biofuel emulsion,” Renew. Sustain. Energy Rev., vol. 52, pp. 1566–1579, Dec. 2015.
[13] A. V. Bueno, M. P. B. Pereira, J. V. de Oliveira Pontes, F. M. T. de Luna, and C. L. Cavalcante, “Performance and emissions characteristics of castor oil biodiesel fuel blends,” Appl. Therm. Eng., vol. 125, pp. 559–566, Oct. 2017.
[14] M. L. Randazzo and J. R. Sodré, “Cold start and fuel consumption of a vehicle fuelled with blends of diesel oil–soybean biodiesel–ethanol,” Fuel, vol. 90, no. 11, pp. 3291–3294, Nov. 2011.
[15] B.-F. Lin, J.-H. Huang, and D.-Y. Huang, “Experimental study of the effects of vegetable oil methyl ester on DI diesel engine performance characteristics and pollutant emissions,” Fuel, vol. 88, no. 9, pp. 1779–1785, Sep. 2009.
[16] S. Vellaiyan and K. S. Amirthagadeswaran, “Taguchi-Grey relational-based multi-response optimization of the water-in-diesel emulsification process,” J. Mech. Sci. Technol., vol. 30, no. 3, pp. 1399–1404, Mar. 2016.
[17] Y. Devarajan, D. B. Munuswamy, A. Mahalingam, and B. Nagappan, “Performance, Combustion, and Emission Analysis of Neat Palm Oil Biodiesel and Higher Alcohol Blends in a Diesel Engine,” Energy & Fuels, vol. 31, no. 12, pp. 13796–13801, Dec. 2017.
[18] Y. Devarajan, D. B. Munuswamy, B. Nagappan, and A. K. Pandian, “Performance, combustion and emission analysis of mustard oil biodiesel and octanol blends in diesel engine,” Heat Mass Transf., vol. 54, no. 6, pp. 1803–1811, Jun. 2018.
[19] O. Aboelazayem, N. S. El-Gendy, A. A. Abdel-Rehim, F. Ashour, and M. A. Sadek, “Biodiesel production from castor oil in Egypt: Process optimisation, kinetic study, diesel engine performance and exhaust emissions analysis,” Energy, vol. 157, pp. 843–852, Aug. 2018.
[20] S. Vellaiyan and K. Amirthagadeswaran, “Multi-response optimization of diesel engine operating parameters running with water-in-diesel emulsion fuel,” Therm. Sci., vol. 21, no. 1 Part B, pp. 427–439, 2017.
[21] S. Vellaiyan, “Enhancement in combustion, performance, and emission characteristics of a diesel engine fueled with diesel, biodiesel, and its blends by using nanoadditive,” Environ. Sci. Pollut. Res., vol. 26, no. 10, pp. 9561–9573, Apr. 2019.
[22] H. Watanabe, Y. Suzuki, T. Harada, Y. Matsushita, H. Aoki, and T. Miura, “An experimental investigation of the breakup characteristics of secondary atomization of emulsified fuel droplet,” Energy, vol. 35, no. 2, pp. 806–813, Feb. 2010.
[23] A. M. Ithnin, M. A. Ahmad, M. A. A. Bakar, S. Rajoo, and W. J. Yahya, “Combustion performance and emission analysis of diesel engine fuelled with water-in-diesel emulsion fuel made from low-grade diesel fuel,” Energy Convers. Manag., vol. 90, pp. 375–382, Jan. 2015.
[24] S. Vellaiyan and C. M. A. Partheeban, “Combined effect of water emulsion and ZnO nanoparticle on emissions pattern of soybean biodiesel fuelled diesel engine,” Renew. Energy, vol. 149, pp. 1157–1166, Apr. 2020.
[25] S. Vellaiyan and K. S. Amirthagadeswaran, “Influence of Water-in-Diesel Emulsion Fuel and Compression Ratio on Combustion, Performance and Emission Characteristics of Diesel Engine,” J. Sustain. Energy Eng., vol. 3, no. 3, pp. 238–253, Feb. 2016.
[26] A. M. Ithnin, H. Noge, H. Abdul Kadir, and W. Jazair, “An overview of utilizing water-in-diesel emulsion fuel in diesel engine and its potential research study,” J. Energy Inst., vol. 87, no. 4, pp. 273–288, Nov. 2014.
[27] A. K. Wamankar, A. K. Satapathy, and S. Murugan, “Experimental investigation of the effect of compression ratio, injection timing & pressure in a DI (direct injection) diesel engine running on carbon black-water-diesel emulsion,” Energy, vol. 93, pp. 511–520, Dec. 2015.
[28] A. K. Hasannuddin et al., “Durability studies of single cylinder diesel engine running on emulsion fuel,” Energy, vol. 94, pp. 557–568, Jan. 2016.
[29] S. Vellaiyan, K. S. Amirthagadeswaran, and S. Vijayakumar, “Combustion of stable water-in-diesel emulsion fuel and performance assessment,” Energy Sources, Part A Recover. Util. Environ. Eff., vol. 39, no. 5, pp. 505–513, Mar. 2017.
[30] M. E. A. Fahd, Y. Wenming, P. S. Lee, S. K. Chou, and C. R. Yap, “Experimental investigation of the performance and emission characteristics of direct injection diesel engine by water emulsion diesel under varying engine load condition,” Appl. Energy, vol. 102, pp. 1042–1049, Feb. 2013.
[31] A. Alahmer, J. Yamin, A. Sakhrieh, and M. A. Hamdan, “Engine performance using emulsified diesel fuel,” Energy Convers. Manag., vol. 51, no. 8, pp. 1708–1713, Aug. 2010.
[32] J. W. Park, K. Y. Huh, and J. H. Lee, “Reduction of NO x , smoke and brake specific fuel consumption with optimal injection timing and emulsion ratio of water-emulsified diesel,” Proc. Inst. Mech. Eng. Part D J. Automob. Eng., vol. 215, no. 1, pp. 83–93, Jan. 2001.
[33] J. Ghojel, D. Honnery, and K. Al-Khaleefi, “Performance, emissions and heat release characteristics of direct injection diesel engine operating on diesel oil emulsion,” Appl. Therm. Eng., vol. 26, no. 17–18, pp. 2132–2141, Dec. 2006.
[34] K. Kannan and M. Udayakumar, “NOx and HC emission control using water emulsified diesel in single cylinder diesel engine,” J. Eng. Appl. Sci., 2009.
[35] A. C. Matheaus, T. W. Ryan, D. Daly, D. A. Langer, and M. P. B. Musculus, “Effects of PuriNOxTM Water-Diesel Fuel Emulsions on Emissions and Fuel Economy in a Heavy-Duty Diesel Engine,” Oct. 2002.
[36] H. Raheman and S. Kumari, “Combustion characteristics and emissions of a compression ignition engine using emulsified jatropha biodiesel blend,” Biosyst. Eng., vol. 123, pp. 29–39, Jul. 2014.
[37] K. Kandasamy and G. Rakkiyanna, “Thevetia Peruviana biodiesel emulsion used as a fuel in a single cylinder diesel engine reduces NOx and smoke,” Therm. Sci., vol. 15, no. 4, pp. 1185–1191, 2011.
[38] G. R. Kannan and R. Anand, “Experimental investigation on diesel engine with diestrol–water micro emulsions,” Energy, vol. 36, no. 3, pp. 1680–1687, Mar. 2011.
[39] V. Perumal and M. Ilangkumaran, “Water emulsified hybrid pongamia biodiesel as a modified fuel for the experimental analysis of performance, combustion and emission characteristics of a direct injection diesel engine,” Renew. Energy, vol. 121, pp. 623–631, Jun. 2018.
[40] I. Jeong, K.-H. Lee, and J. Kim, “Characteristics of auto-ignition and micro-explosion behavior of a single droplet of water-in-fuel,” J. Mech. Sci. Technol., vol. 22, no. 1, pp. 148–156, Jan. 2008.
[41] J. Sadhik Basha and R. B. Anand, “Performance, emission and combustion characteristics of a diesel engine using Carbon Nanotubes blended Jatropha Methyl Ester Emulsions,” Alexandria Eng. J., vol. 53, no. 2, pp. 259–273, Jun. 2014.
[42] J. Jeevahan, G. Mageshwaran, G. B. Joseph, R. B. D. Raj, and R. T. Kannan, “Various strategies for reducing No x emissions of biodiesel fuel used in conventional diesel engines: A review,” Chem. Eng. Commun., vol. 204, no. 10, pp. 1202–1223, Oct. 2017.
[43] D. H. Qi, H. Chen, R. D. Matthews, and Y. Z. Bian, “Combustion and emission characteristics of ethanol–biodiesel–water micro-emulsions used in a direct injection compression ignition engine,” Fuel, vol. 89, no. 5, pp. 958–964, May 2010.
[44] B. K. Debnath, N. Sahoo, and U. K. Saha, “Adjusting the operating characteristics to improve the performance of an emulsified palm oil methyl ester run diesel engine,” Energy Convers. Manag., vol. 69, pp. 191–198, May 2013.
[45] M. Tsue, D. Segawa, T. Kadota, and H. Yamasaki, “Observation of sooting behavior in an emulsion droplet flame by planar laser light scattering in microgravity,” Symp. Combust., vol. 26, no. 1, pp. 1251–1258, Jan. 1996.
[46] J. G. T. Reyes and E. N. Quiros, “Determination of the Start and End of Combustion in a Direct Injection Diesel Engine Using the Apparent Heat Release Rate,” Jun. 2017.
[47] J. Pain, “Gas Dynamics,” Nature, vol. 213, no. 5082, p. 1182, 1967.
[48] H. G. How, H. H. Masjuki, M. A. Kalam, Y. H. Teoh, and H. G. Chuah, “Effect of Calophyllum Inophyllum biodiesel-diesel blends on combustion, performance, exhaust particulate matter and gaseous emissions in a multi-cylinder diesel engine,” Fuel, vol. 227, pp. 154–164, Sep. 2018.